Single Retorquer
April 23, 2021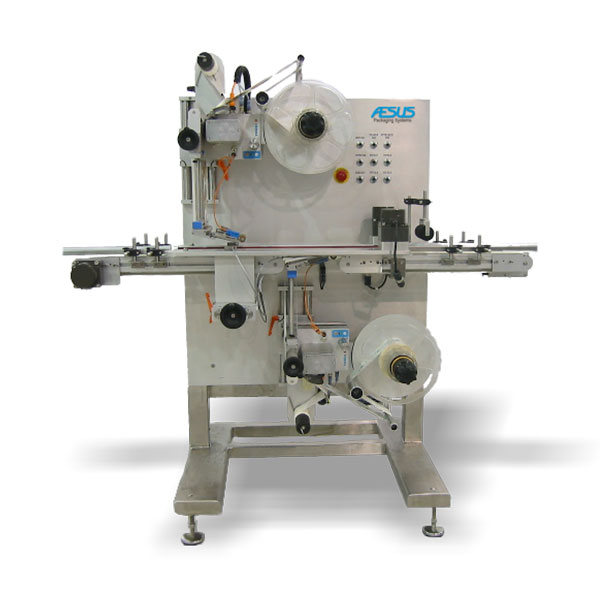
Delta Top and or Bottom Labeler
May 3, 2021Aesus Premier Shrink Sleeving Machine
The Aesus Premier shrink sleeving machine has a larger cabinet than the Delta Model and has higher speeds due to larger and more rugged servo drives.
Multiple Blades spin around the mandrel to-part the sleeve before application to the neck or container, and then the sleeve is fired onto the container or neck as the product is presented below. A Servo feed mechanism in conjunction with servo blades cut the sleeve.
The Premier Shrink Labelerboasts speeds in excess of 400 minute with a single head.
As with our Premier range of labelers the Premier Shrink Labeler is highly customizable according to client needs.
Request Product Updates
Premier Shrink Multi Blade
The Premier Shrink also has a servo multiple blade system that parts off the sleeve on its mandrel before applying it to the neck or container. When the container is underneath the mandrel the servo controlled feed system spins the sleeve onto the container.
The Cutting Assembly can be slid out of the machine for blade replacement, service, or adjustment. Some customers have a standby unit ready to slide in, in the unlikely event of trouble.
Optional for high speed machines: A dual powered unwinder with accumulation bin and splicing station to allow uninterupted production while the large sleeve rolls are being exchanged.
Changeover: new products can be set up quickly and easily. The time saved adds up rapidly… helping pay for the machine over and over.
Noteworthy
We use Powerful Servo and not Stepper drives to feed the band, and to power the cutting blades.
User Freindly controls
A large touch screen operator panel shows machine status, controls all options, has memories to recall previous set-ups, and is password protected if requested.
Features
Speeds up to 400 bpm (dependent on container’s characteristics) Dual units at twice the speed
Power unwind of the band material
Powerful Servo motor drives the band material down the mandrel that keeps the Band open until it is on the container.
No tricky transfer mechanism. Exclusive Servo driven Rotary knife assembly cuts the sleeve material 360° around the mandrel. In between each cut, the servo driven knife assembly is phased in and then away from the mandrel.
The rotary knife is fully adjustable. Competitive machines require that you purchase an additional assembly for each varying container diameter.
Worm or Starwheel bottle separation. The band material is cut and applied without stopping the bottles. High speed fiber optic sensors detect the presence of the container, and the machine then applies the band material.
Extremely high efficiency.** Dual servo driven wheels assist in applying the cut sleeve onto the bottles at high speed
Allen Bradley high speed PLC;Allen Bradley Panelview Plus 1000 color touchscreen
Variable stroke, complete with height-adjustable stand, fully interlocked Lexan and stainless steel tube guarding for added operator safety
Automatic Motorized Band Unwind, operates using a low level sensor which detects when the band unwind should feed band to alleviate web tension
Optional Accessories
Photo Registration for Printed Band Material, stops the feed at the length determined by photo registration marks on the Material.
Automatic Motorized Band Unwind, operates using a low level sensor which detects when the band unwind should feed band to alleviate web tension.
Vertical Perforation Assembly, always combined with the motorized band unwind, a hardened perforation wheel perforates the sleeve. Note with our system no additional tension is given to the web by the perforation wheel because of the motorized unwind. The Perforation placement on the band can be adjusted anywhere horizontally along the material’s layflat.
Horizontal Perforation Assembly Allowing the cap to be removed from the container while leaving the sleeve on the the container.