Single Retorquer
April 23, 2021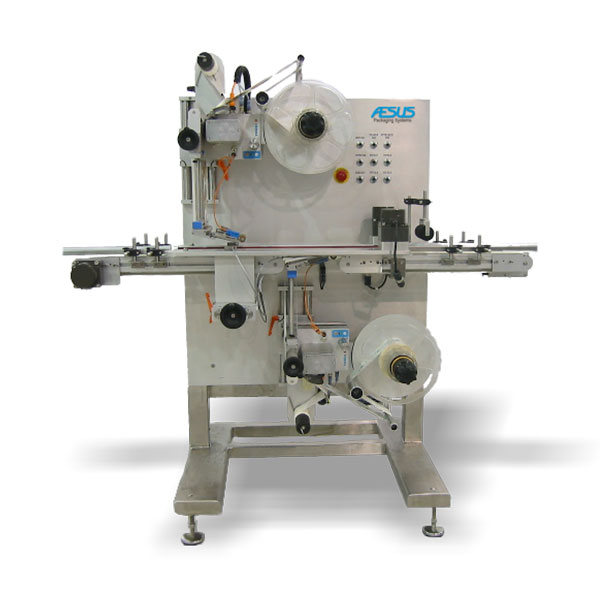
Delta Top and or Bottom Labeler
May 3, 2021Rotary Rollfed Labeler
Wrap around film labels from a roll of labels with hot melt
The GERNEP ROLLFED labelling machine has novel patented hot melt gluing technology for wrap around labelling of containers with the price advantage of film labels from a roll.
The reduced glue usage and minimised cleaning times resulting from contact-free gluing means that the GERNEP ROLLFED is the economical answer to the increasing labelling demands in the beverage, food and chemical industries.
Clear, ergonomic controls provide for problem free operation. Changeover and cleaning times are reduced to a minimum.
The modular design of our machine means that several H400 self-adhesive heads can be flexibly located around the bottle carousel and if required also a glue labelling station can be attached.
Labelling machines with unmistakable performance.
Request Product Updates
The H400 label feed unit transports the labels using its servo motor to feed the film(label) to an exact cutting position which is registered positively by the photoelectric sensors. A special variable speed transmission eases the label positioning on the vacuum drum and hence onto the bottle table which enormously reduces complicated electronic synchronisation.
This labelling machine is designed for ease of operation and to be highly reliable thanks to control electronics which ensure optimum glue dosing and providing for the possibility for preprogramming different bottle labelling.
Contact-free: The GERNEP ROLLFED only fixes the label on the container at the beginning and end of the label with hot glue spots ensuring economic use of glue at the same time as ensuring firm label adhesion. The gluing is contact-free direct onto the label while it is on the transfer drum both at the start and end of the label. If the label is to be glued right up to the final label edge, this can be done by a height adjustable end gluing bar.
A pull out slide can be provided for each Label head for user friendly reel change and better machine accessibility.
The simple changeover to other formats and label positioning is easy to understand with a menu guide.
Speed range : 50 to 500 per minute. The labelling machines are customer driven solutions adapted to the speed and size. Hence we produce small and compact machines for lower speeds right up to high performance machines over a whole range of equipment configurations.
Containers: PET containers or other plastic
Gluing system: Hot melt glue
Professionalism
How it works
• The in-feed star 2 passes the bottle to the bottle table 3 . The bottles are held in position between the plate and self-centring punch and mechanically rolled into the correct labelling position.
• The bottles are sprayed with hot glue through the heated nozzles of the glue station 4 without contact.
• From the powered unrolling station for the label rolls 5 (spare roll 6) via many spring-loaded tension rollers, the label is guided to electronic scanning. The spring-loaded tension rollers ensure continuous feed.
• Electronic sensor 7 is used to position the label accurately on the cutting drum by means of a servo motor 8 .
• Finely ground blades on the cutting drum 9 ensure exact cutting and separation of the labels.
• After cutting, they are passed to the vacuum transfer drum 10 which transfers the label directly to the glue zone on the bottle.
• The end of label is glued on the vacuum drum 11 by means of a narrow, continuous vertical strip of glue.
• The end of the label is pressed by a brush section so that it is fixed solidly 12 .
• The heating of the glue and the perfect proportioning takes place in a separate glue management unit 13 with its own electronic control unit.
• The labelled bottles are transferred to the conveyor 15 through the out-feed star 14 .
Features
Start of label gluing: Through non-contact glue application via heated nozzles directly on the container.
End of label gluing: Through a continuous strip of glue on the label that has just been attached to the bottle .
Exact cut
The label is fixed in position on the cutting drum by low pressure and then transferred to a vacuum drum for gluing.
The ROLLFED Glue Management System
The ROLLFED glue management system consists of an independent unit that is integrated into the labelling machine with its own electronic control unit. The functions such as hot zones, glue temperature, and glue dosing are simply entered using selector keys. The status of the device is shown reliably using illuminated displays.
Non-contact gluing at the edges
The GERNEP ROLLFED fastens the label to the container only at the start and end of the label with hot glue and that way guarantees economical glue consumption with a firmly affixed label.
Due to the the innovative gluing system, the glue for the label start is applied directly to the container.
TThe vacuum drum is only used to glue the end of the label only when the beginning of label is already fixed onto the hot adhesive that is on the bottle.
The Control Units –
The control units of the GERNEP ROLLFED is split into the machine control unit,H400 labelling head control unit, and glue management control unit. This way, the operational reliability and simplicity is increased considerably.
Only brand name components that have been tried and proven umpteen thousand times are used in the electronics.
Operation – Easy and Logical
We consciously kept the ROLLFED as simple as possible. Different label lengths are set in seconds using a micrometer with a counter.
Control of Bottle Plates
The control of the bottle plates varies with machine type.
Mechanically via cam segments…. or
With a timing belt that controls the rotation of the bottle plate.
or… utilising Servo motors located at each bottle plate.
The latter allows a recallable program to rotate every container size to suit, ensuring perfect application of the labels for each set up.
Mechanical container aligner
The container aligner has special alignment systems to guarantee an exact alignment of the container.
Flexible and cost-effective
The ROLLFED labelling system can be easily and cost-effectively retrofitted for other bottle designs.
The rotary table is divided into segments so that labour-intensive changeover is no longer required, and often not all the cams need to be changed.
Bottle alignment, hot glue assembly and coders etc can be added at any time.
Label monitoring
Sensor based and/or a camera based system can check the presence and alignment of labels on containers of all types. Bottles where labels are incorrect can be rejected accordingly.